Biosensors Continuous monitoring of water biofilm
Innovate, Incubate, Industrialize
Industry 4.0
Real-Time Bacteria Detection Solutions with EGIDION's Biofilm Sensors
Biofilm phenomenon, characterized by bacterial growth on internal surfaces of pipes and tanks in contact with water and other liquids, poses significant challenges across various industries. At EGIDION, we offer a cutting-edge digital online-monitoring solution for continuous biofilm prevention and detection.
Our technology utilizes Biological Electrochemical Signal (BES) to effectively prevent biofilm growth by indicating bacterial coverage on surfaces in real-time, enabling proactive measures against potential risks.
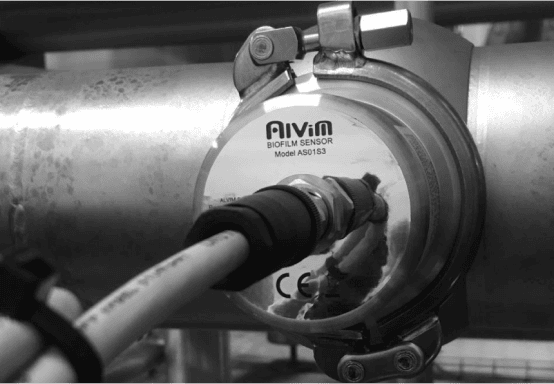
BIOFILM: Understanding Its Structure and Importance for Biofilm Sensors
A biofilm is a thin yet resilient layer of mucilage adhering to a solid surface, harboring a community of bacteria and other microorganisms. Within the piping system, biofilms are prevalent, with planktonic cells representing less than 10% of all bacteria in liquid.
Comprising a syntrophic consortium of microorganisms, biofilms consist of cells adhering to each other and often to a surface. These adherent cells are embedded within a slimy extracellular matrix, primarily composed of extracellular polymeric substances.
Planktonic cells
Free floating bacteria in liquid represents less than 10% of all bacteria in the piping system
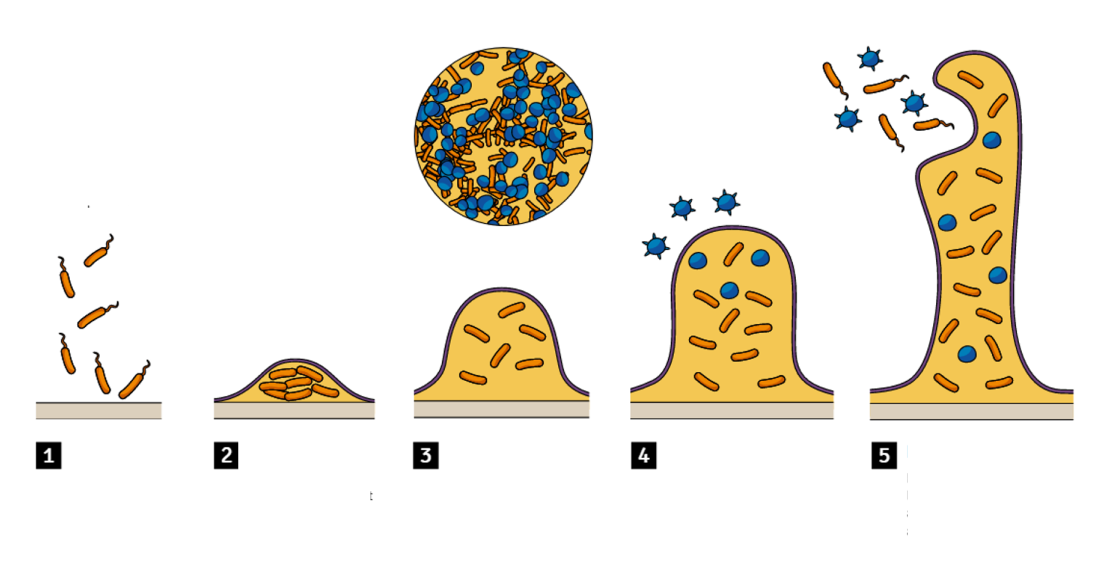
- Reversible Attachment Attachment of bacteria to surface
- Irreversible Attachment Formation of layer and production of matrix, forming of EPS -Extracellular polymeric substances
- Growth Microcolony formation, multilayer
- Maturation Microcolony, mature biofilm with characteristic mushroom formed of polysaccharide
- Dispersal Detachment and reversion to platonic growth, starting the new cycle e
biofilm
It is a thin but a robust layer of mucilage adhering to a solid surface and containing a community of bacteria and other microorganizms.
Planktonic cells
Free floating bacteria in liquid represents less than 10% of all bacteria in the piping system
A biofilm comprises any syntrophic consortium of microorganisms in which cells stick to each other and often also to a surface.
These adherent cells become embedded within a slimy extracellular matrix that is composed of extracellular polymeric substance
Reversible Attachment
Attachment of
bacteria to
surface
Irreversible Attachment
Formation of layer
and production of
matrix, forming of
EPS -Extracellular
polymeric
substances
Growth
Microcolony
formation, multilayer
Maturation
Microcolony, mature
biofilm with
characteristic
mushroom formed of
polysaccharide
Dispersal
Detachment and
reversion to platonic
growth, starting the
new cycle
Understanding the Impact of Bacterial Biofilm Development and the Role of Biofilm Sensors
Bacterial biofilm development in fluid environments poses numerous challenges, including corrosion, equipment failure, energy loss, reduced performance, increased energy consumption, and resistance to antimicrobial treatments. These issues can escalate, leading to pipe blockage and plant downtime.
Early intervention is crucial. Sanitation treatments should be applied promptly upon biofilm detection, as mature biofilms are more difficult and costly to eradicate due to their thicker extracellular polymeric substance (EPS) matrix, rendering them highly resistant.
Mature biofilms pose additional risks as their outer layers detach and spread, potentially contaminating other areas of the plant. Standard laboratory analysis and bacteria detection kits have limitations, as they are time-consuming and may not accurately represent bacterial abundance, given that most bacteria reside within biofilms rather than free in the fluid.
To mitigate the risk of dangerous bacterial contamination, immediate biofilm detection is imperative. Biofilm sensors play a pivotal role in monitoring biofilm formation, enabling proactive intervention to minimize risks and ensure operational efficiency.

BIOFILM SENSOR: Unlocking Industry Applications and ROI Potential
Our cutting-edge biofilm sensor system offers rapid return on investment (ROI) across various industrial sectors. Industrial plants can achieve ROI of up to 100% in just one month, while Food & Beverage production plants can see returns of 100% in one week. Power plants affected by biofilm growth can experience daily ROI of 100%.
Our technology delivers numerous benefits, including significant reductions in chemical usage, enhanced microbiological safety, prevention of customer complaints, and improved heat-exchange efficiency. In power plants, these advancements can boost production by up to 30%.
Our biofilm sensors find applications across diverse industries, including food production, soft drink production, water distribution networks, mineral water bottling, Legionella prevention, power plant water treatment, cooling tower water treatment, once-through cooling systems, industrial reverse osmosis, reverse osmosis desalination, and pulp and paper manufacturing.
By harnessing the power of biofilm sensors, industries can optimize operations, improve efficiency, and ensure the highest standards of safety and performance.
- Food production
- Soft drink production
- Water Distribution Networks
- Mineral water bottling
- Legionella prevention
- Power plant water treatment
- Cooling tower water treatment
- Cooling towers and bacteria
- Once-through cooling systems
- Industrial reverse osmosis
- Reverse osmosis desalination
- Pulp and paper
- Biogas upgrading plants
4 types of biofilm sensors for different applications
Our sensors monitor the bio-electrochemical signal produced by bacteria. This signal is directly linked to the biological activity of bacteria, and it is proportional to the surface area covered by biofilm. Therefore, the system monitors just living bacteria, not other kinds of fouling (e.g. mineral deposit, fats, proteins, etc.).
A Biofilm Monitoring System includes one or more sensors, connected to a data acquisition system (PLC, DCS, PC, etc.) through the standard communication protocols like RS485 MODBUS and 4-20 mA.
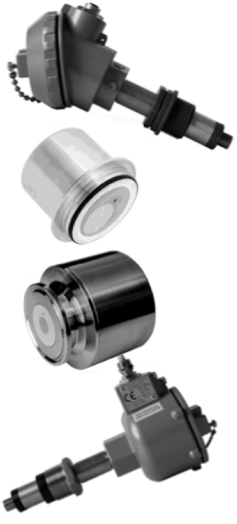
A001S3 probe, for highly corrosive environments, moderate heat and chemical resistance.
AS01S3 andAS11S3 (with clamp connection), with hygienic connection to the process, flat surface in contact with the liquid and high resistance to chemical treatments, this model is indicated for applications where hygiene is critical.
AX03S3, ATEX certified, this model is indicated for classified areas and applications where there is a risk of explosion (e.g. Oil&Gas).
Industry Solutions:
Optimizing Biofilm
Sensor
Implementation
Beginning with idea validation and crafting the customer journey, to solution testing, piloting, and proficiently managing scaling processes, we offer a holistic IoT service design approach tailored specifically for biofilm sensor applications. Our adept team harnesses design thinking and value proposition design methodologies to meticulously align every facet of the solution with the unique requirements and expectations of our clients in the biofilm sensing domain.